在工业自动化、流体传输及测试领域,快速密封连接器作为关键部件,其性能直接影响生产效率与系统可靠性。随着工业设备对流量需求不断提升,快速密封连接器能否适应大流量场景成为行业关注的焦点。本文将从技术原理、结构设计、材料应用及实际案例出发,探讨其在大流量环境中的适应性。
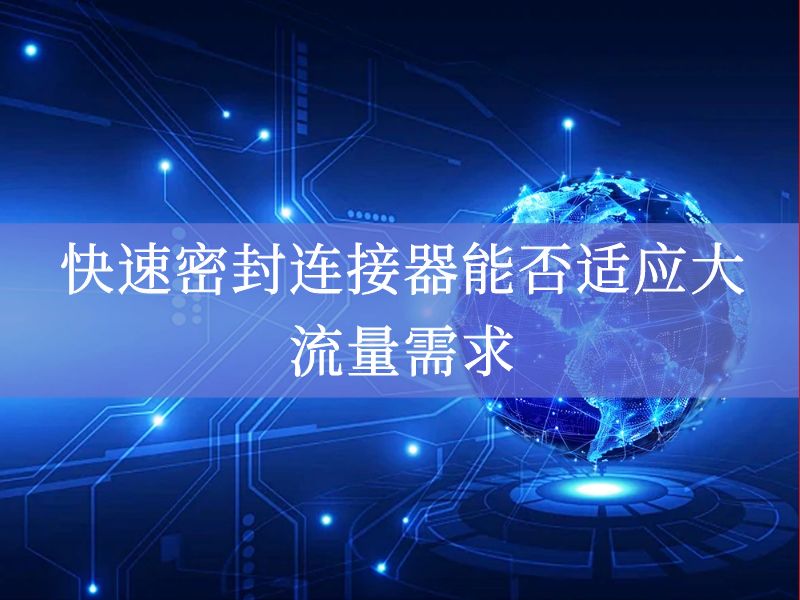
一、大流量需求的技术挑战
大流量场景对连接器的核心要求包括:低流阻、高密封性及长期稳定性。传统连接器因结构限制,可能存在以下问题:
流道设计缺陷:内部通道狭窄或存在直角弯折,导致流体阻力增加,流量受限。
密封件磨损:高速流体冲击下,密封圈易变形或老化,引发泄漏风险。
热膨胀影响:高流量下流体摩擦生热,可能导致材料膨胀或结构变形,破坏密封性。
为应对这些挑战,现代快速密封连接器需通过优化流道设计、增强密封结构及选用耐高温材料,实现流量与密封性的平衡。
二、技术原理与结构创新
1. 流道优化设计
大流量连接器通常采用直通式流道设计,减少内部弯折与障碍物。例如,部分产品通过扩大中心杆直径或采用渐变式流道,使流体通过时阻力降低30%以上。此外,流道表面经过抛光处理,进一步减少摩擦损失。
2. 密封机制升级
密封性能是大流量场景的核心指标。当前主流技术包括:
动态密封圈:采用高弹性材料(如聚氨酯或硅橡胶),在流体压力下自动调整形变,确保密封面贴合度。
多级密封结构:通过主密封圈与辅助密封圈的组合,分担压力负荷,延长使用寿命。
气压辅助密封:部分产品通过驱动孔注入压缩空气,推动活塞挤压密封圈,实现内胀式密封,适用于光滑管壁或螺纹接口。
3. 材料与工艺突破
为适应高温高压环境,连接器主体多采用铝合金或不锈钢材质,兼具轻量化与抗腐蚀性。密封圈材料则根据介质特性选择:
氯丁橡胶:耐油性优异,适用于液压系统。
丁腈橡胶:耐磨性强,适合含颗粒流体。
氟橡胶:耐高温(可达200℃),适用于蒸汽或化学介质。
三、实际应用中的性能验证
1. 工业自动化生产线
在汽车零部件测试中,连接器需承受每分钟数百次的插拔操作,同时保证流量稳定。某案例中,某型连接器通过优化密封圈结构,将泄漏率控制在0.01ml/min以下,并支持连续10万次插拔无性能衰减。
2. 流体传输系统
在石油管道或冷却水系统中,连接器需应对高压与大流量冲击。某企业采用直通式流道设计,使流量提升50%,同时通过内置限位环防止密封圈过载,确保长期可靠性。
3. 气密性测试场景
在传感器或阀门测试中,连接器需在1-3MPa压力下实现瞬时密封。某型号通过气压驱动密封圈膨胀,1秒内完成连接,且泄漏率低于行业标准。
四、关键参数与选型指南
1. 流量接口规格
大流量连接器通常提供多种接口选项(如G1/8、G1/4螺纹孔),用户需根据系统流量需求选择匹配的接口尺寸。
2. 操作压力范围
主流产品支持真空至8Bar压力,部分型号可扩展至更高压力,需根据介质特性与系统工况选择。
3. 密封范围与插入深度
连接器需适配不同管径(如8.5mm-35mm),插入深度一般为15-30mm,需确保与被测件完全贴合。
4. 维护便捷性
快速更换密封圈的设计可缩短停机时间。例如,某产品通过弹出式弹簧组件,3步即可完成密封圈更换。
五、未来发展趋势
智能化集成:部分产品已集成压力传感器与温度监测模块,实现实时状态反馈。
模块化设计:通过标准化接口与可扩展组件,满足不同场景的定制化需求。
环保材料应用:生物基橡胶或可降解材料的应用,降低对环境的影响。
六、结论
快速密封连接器通过流道优化、密封机制升级及材料创新,已具备适应大流量场景的能力。在工业自动化、流体传输及测试领域,其高效、可靠的特性显著提升了生产效率与系统安全性。未来,随着智能化与模块化技术的进一步发展,快速密封连接器将在更多高要求场景中发挥关键作用。
企业在选型时,需综合考量流量需求、介质特性、操作压力及维护成本,选择技术成熟、口碑可靠的产品。同时,定期维护与规范操作是保障连接器长期稳定运行的关键。通过科学选型与合理使用,快速密封连接器将成为工业流体系统中不可或缺的“流量守护者”。