食品加工行业对生产设备及连接部件的卫生要求极为严格,快速密封连接器作为管道、阀门等设备的关键连接部件,其卫生性能直接影响食品安全与生产效率。本文结合行业规范与技术实践,探讨快速密封连接器在食品加工领域的卫生标准及实施要点。
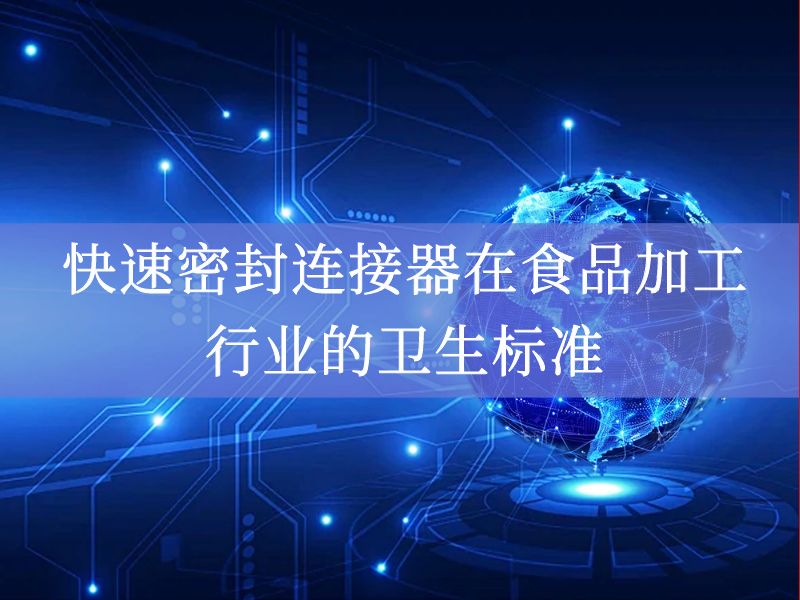
一、材料选择与耐腐蚀性要求
食品加工环境中的介质多样,包括酸碱溶液、油脂、高温蒸汽等,这对连接器的材料性能提出双重挑战。首先,材料需具备食品级安全认证,例如符合相关法规的聚四氟乙烯、不锈钢等材质,避免重金属析出或有害物质迁移。其次,材料需通过耐腐蚀性测试,例如在30%浓度氢氧化钠溶液中浸泡72小时后,表面无腐蚀、无脱落,确保在强酸碱环境下仍能维持结构完整性。此外,材料还需通过生物相容性测试,如细胞毒性实验、致敏性测试等,确保与食品接触时不会引发污染风险。
二、密封结构与流体控制
快速密封连接器的核心功能是实现流体传输的零泄漏,其密封结构需满足双重标准。一方面,O型密封圈需采用高弹性硅胶或氟橡胶材质,在-40℃至200℃范围内保持弹性,确保在高压蒸汽灭菌或低温冷藏场景下仍能紧密贴合管壁。另一方面,平面密封面需达到镜面级光洁度,表面粗糙度Ra≤0.4μm,配合压力锁紧装置,在1.5倍工作压力下保持密封性。例如,在乳制品输送系统中,连接器需承受10bar压力,且泄漏率≤0.1ml/min,避免微生物通过缝隙侵入。
三、表面处理与清洁验证
食品加工设备的清洁难度直接影响生产效率,连接器的表面处理需兼顾耐磨性与易清洁性。常见工艺包括电解抛光、阳极氧化等,可使表面粗糙度降低至Ra≤0.2μm,减少污垢附着。清洁验证需通过模拟生产测试,例如在巧克力浆料输送后,使用CIP(原地清洗)系统以80℃碱液循环冲洗15分钟,再通过ATP生物荧光检测,确保表面菌落总数≤10CFU/cm?。此外,连接器需设计为无死角结构,避免螺纹、缝隙等藏污纳垢区域,例如采用快拆式卡扣替代传统螺纹连接。
四、安装与维护规范
错误的安装操作是导致密封失效的主要原因,需制定标准化流程。安装前需检查密封圈完整性,使用专用工具确保对接精度,例如在果汁灌装线中,连接器轴向偏差需控制在±0.1mm以内。维护周期需根据介质特性设定,例如输送高糖分饮料时,建议每200小时检查密封圈压缩量,当压缩量减少15%时需更换。拆卸后需进行彻底清洁,例如使用超声波清洗机去除油脂残留,再通过高压蒸汽灭菌(121℃、30分钟)确保无菌状态。
五、行业应用案例与验证
在乳制品行业,某企业采用高洁净度连接器后,巴氏杀菌机管道泄漏率下降90%,年维护成本减少60万元。在饮料灌装线中,通过优化连接器密封结构,CIP清洗时间缩短40%,水耗降低25%。某调味品企业引入耐腐蚀连接器后,酱油输送管道的微生物污染事件减少85%,产品保质期延长3个月。这些案例表明,符合卫生标准的连接器可显著提升生产效率与产品质量。
六、未来技术发展趋势
随着食品加工自动化程度提升,连接器正朝着智能化、模块化方向发展。例如,集成压力传感器的智能连接器可实时监测密封状态,当泄漏风险超过阈值时自动报警;模块化设计支持快速更换密封组件,将维护时间从2小时缩短至15分钟。此外,新型抗菌涂层技术(如银离子掺杂)可抑制微生物附着,使连接器表面菌落总数降低至5CFU/cm?以下。
七、法规遵循与认证体系
食品加工企业需确保连接器符合国内外法规,例如通过相关标准认证,证明材料无毒无害、结构无卫生死角。此外,连接器供应商需提供完整的材质报告、清洁验证文件及使用寿命测试数据,例如在模拟工况下完成10万次插拔测试后,密封性能仍满足标准。企业应建立连接器管理档案,记录采购、安装、维护、报废全生命周期信息,确保可追溯性。
八、成本效益分析
虽然符合卫生标准的连接器初期采购成本较高,但长期效益显著。例如,某烘焙企业更换连接器后,因管道泄漏导致的原料浪费减少70%,设备停机时间减少50%,综合成本降低35%。此外,符合卫生标准的连接器可提升企业通过认证的概率,增强市场竞争力。
快速密封连接器在食品加工行业的卫生标准涉及材料、设计、工艺、维护等多个维度。企业需从全生命周期角度评估连接器性能,选择符合法规要求、具备可验证性的产品,并通过标准化管理确保其持续有效运行。未来,随着技术进步与法规完善,连接器将在保障食品安全、提升生产效率方面发挥更大作用。