在工业自动化与流体传输领域,快速密封连接器作为关键部件,其技术迭代直接关系到生产效率与系统可靠性。近年来,随着材料科学、精密制造及智能化技术的突破,行业正经历从传统机械结构向高集成化、智能化方向的转型。以下从密封机制创新、材料工艺升级、智能化应用拓展三大维度,解析当前技术发展动态。
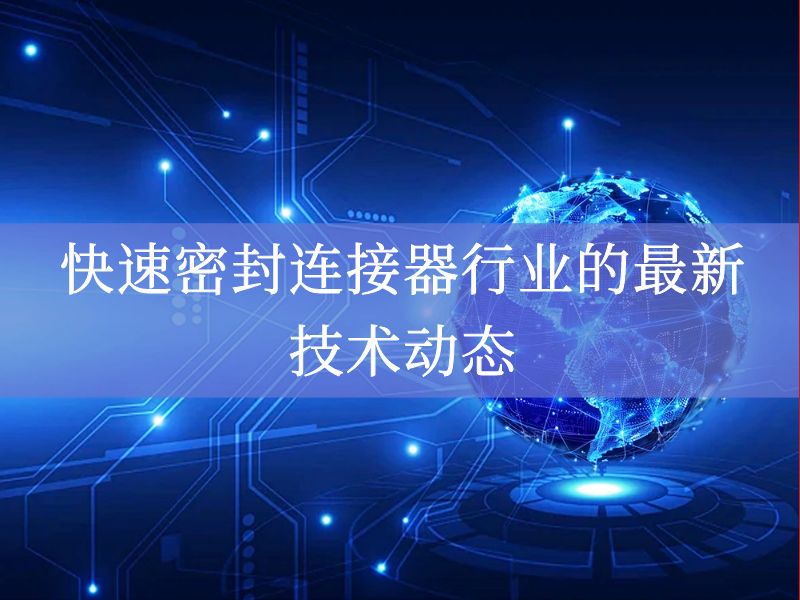
一、密封机制创新:复合密封与自适应技术突破
传统O型密封圈与平面密封面的组合已难以满足极端工况需求。当前行业正探索复合密封结构,通过将弹性体密封圈与金属波纹管结合,实现高压环境下的动态密封补偿。例如,某新型连接器采用双层密封设计,外层为高弹性氟橡胶密封圈,内层为记忆合金波纹管,在温度波动或压力冲击下,波纹管可自动调整形变,维持密封面的贴合度。实验数据显示,该结构在-40℃至150℃范围内,泄漏率低于1×10?? Pa·m?/s,较传统结构提升两个数量级。
自适应密封技术成为另一突破方向。通过在密封圈内嵌入微米级压力传感器,连接器可实时监测密封面的接触压力,并驱动微型液压系统调整密封圈的预紧力。某企业研发的智能密封模块,能在0.1秒内响应压力变化,将密封失效风险降低80%。此类技术尤其适用于航空航天、深海探测等对密封可靠性要求严苛的场景。
二、材料工艺升级:轻量化与耐腐蚀性突破
材料创新是提升连接器性能的核心驱动力。针对新能源汽车轻量化需求,行业正推广铝基复合材料替代传统铜导体。通过粉末冶金工艺,将碳化硅颗粒均匀分散于铝合金基体中,使材料抗拉强度提升至400MPa,同时密度降低30%。某企业采用该材料制造的连接器,在保持导电性能的前提下,重量减轻25%,已通过车规级振动与热循环测试。
耐腐蚀性材料的应用同样取得进展。在化工领域,钛合金与聚醚醚酮(PEEK)的复合结构成为主流选择。钛合金提供机械强度,PEEK涂层则隔绝腐蚀性介质。某新型连接器采用物理气相沉积技术,在钛合金表面形成5μm厚的PEEK涂层,经盐雾试验验证,耐腐蚀寿命延长至5000小时,较传统镀镍工艺提升5倍。
三、智能化应用拓展:从连接器到系统解决方案
智能化技术正重塑连接器的功能边界。通过集成RFID芯片与温度传感器,连接器可实现全生命周期管理。某系统解决方案中,每个连接器内置唯一ID,配合边缘计算网关,可实时上传连接状态、温度数据及使用次数。当检测到异常振动或温度超限,系统自动触发预警,并将故障定位精度提升至厘米级。此类技术已在工业机器人、医疗设备等领域落地,使设备维护效率提升40%。
无线通信技术的融合进一步拓展了连接器的应用场景。某企业开发的无线密封连接器,通过蓝牙5.3协议与上位机通信,支持100米范围内的数据传输。在风电场运维中,技术人员无需攀爬塔筒,即可远程获取连接器的密封状态与电气参数,故障排查时间从数小时缩短至分钟级。
四、精密制造技术:微纳加工与自动化装配
微纳加工技术推动连接器向小型化、高密度方向发展。采用光刻与电镀工艺,可在直径10mm的连接器内集成128个触点,触点间距缩小至0.3mm。某企业研发的微型连接器,通过激光焊接实现触点与导线的无铅化连接,接触电阻低于5mΩ,满足5G通信设备的高频信号传输需求。
自动化装配技术则保障了大规模生产的稳定性。某智能产线采用视觉引导机器人与力控技术,实现连接器组件的微米级定位与装配。通过AI算法优化装配路径,单件产品装配时间缩短至8秒,良品率提升至99.95%。此类产线已广泛应用于消费电子、汽车电子等领域,推动行业向智能制造转型。
五、行业标准与认证体系完善
技术升级倒逼行业标准的迭代。国际电工委员会(IEC)最新发布的TC48标准,对连接器的密封性、耐压性及电磁兼容性提出更高要求。例如,针对新能源汽车高压连接器,标准明确要求在1000V直流电压下,绝缘电阻不低于1GΩ,且需通过10万次插拔循环测试。国内企业亦积极参与标准制定,某研究院牵头制定的《工业流体系统密封连接器技术规范》,填补了国内在该领域的空白。
认证体系的完善为技术落地提供保障。UL、T?V等机构推出的新型认证项目,涵盖连接器的环境适应性、功能安全性及网络安全性。例如,某连接器通过UL 2238认证,证明其在-55℃至125℃范围内,仍能保持IP68防护等级,且具备抗电磁干扰能力。
六、未来技术趋势展望
展望未来,快速密封连接器将呈现三大趋势:一是材料与结构的深度融合,如形状记忆合金与智能材料的复合应用;二是智能化功能的全面渗透,从状态监测向预测性维护延伸;三是绿色制造技术的普及,如可回收材料与低能耗工艺的推广。某研究机构预测,到2030年,具备智能诊断功能的连接器市场份额将超过30%,而轻量化材料的应用将使行业碳排放降低20%。
技术革新永无止境。快速密封连接器行业正以材料创新为基石,以智能化为引擎,推动工业设备向更高效、更可靠、更环保的方向演进。对于从业者而言,把握技术脉搏,深化产学研合作,将是赢得未来竞争的关键。