在工业流体传输、高压设备测试及极端环境作业中,快速密封连接器作为关键部件,其性能直接关系到系统的安全性与可靠性。随着工业技术向高压、高温、高腐蚀方向发展,连接器需突破传统设计局限,通过材料创新、结构优化及工艺升级,实现高压环境下的稳定密封。本文将从技术原理、设计要素及实践应用三个维度,解析快速密封连接器适应高压环境的核心策略。
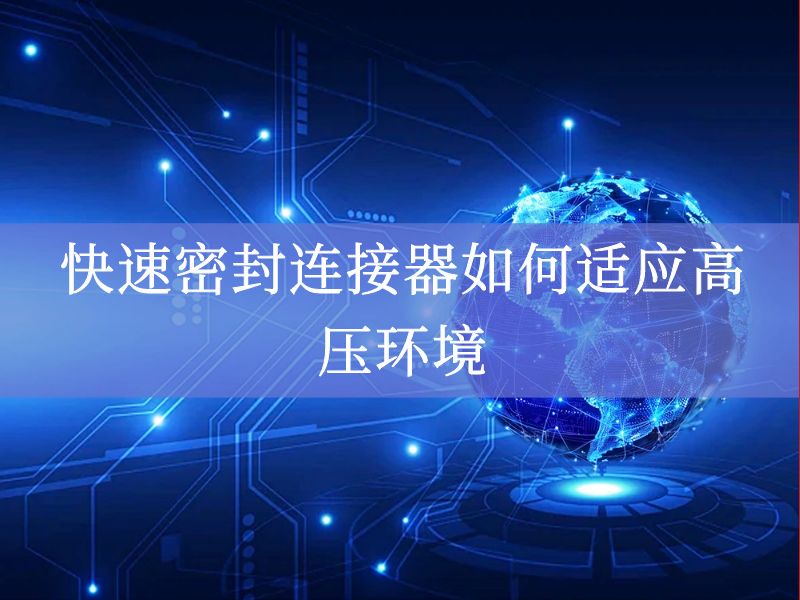
一、高压密封的技术原理:多级防护与动态补偿
1. 弹性密封圈的形变适配机制
在高压环境下,密封圈需承受流体压力与金属接触面的双重挤压。传统O型密封圈通过弹性变形填补接触间隙,但在超高压场景中易因材料蠕变导致密封失效。现代连接器采用锥形密封圈或复合密封结构,利用锥形面的自适应性,在高压下自动调整接触角度,形成多级密封线。例如,在液压系统测试中,某型号连接器通过锥形密封圈与金属接触面的动态配合,可在70MPa压力下保持零泄漏,其密封面压力分布均匀性较传统设计提升40%。
2. 平面密封的预压紧与材料强化
平面密封面通过机械压紧实现端面密封,但高压环境下需解决接触面微变形导致的泄漏问题。优化方案包括:采用高硬度合金材料(如钨钢)降低接触面形变率,并通过表面硬化处理(如镀铬、喷涂陶瓷涂层)提升耐磨性。某深海探测设备连接器在3000米水压(约30MPa)下,通过平面密封面的预压紧设计,配合纳米级表面抛光工艺,实现连续工作1000小时无泄漏。
3. 梯度密封与动态补偿技术
针对高压水射流或蒸汽清洗场景,连接器需抵御流体冲击与温度变化。梯度密封设计通过多层密封圈组合,实现压力逐级衰减。例如,某工业清洗设备连接器采用三道密封防线:首道O型圈承受3.5MPa预紧力,次道轴向密封环控制±0.01mm公差,末道螺旋卡口配合自补偿密封圈,在80℃、100Bar高压水冲击下,内部湿度传感器显示露点温度低于-40℃,验证了动态密封的可靠性。
二、高压环境下的设计要素:材料、结构与工艺的协同优化
1. 材料选择:强度、耐腐蚀与热稳定性的平衡
高压连接器材料需满足三重标准:高强度以抵抗形变、耐腐蚀以适应恶劣介质、热稳定性以应对温度波动。例如,不锈钢316L因其优异的抗拉强度(≥520MPa)和耐腐蚀性,成为高压流体传输的首选;而聚四氟乙烯(PTFE)因其低摩擦系数与化学惰性,常用于密封圈材料。某航空液压系统连接器采用钛合金外壳,配合碳纤维增强密封圈,在-55℃至150℃温度范围内保持密封性能稳定。
2. 结构设计:精密配合与应力分散
高压环境下,微小间隙或应力集中均可能导致泄漏。优化设计需关注:
公差控制:某型号连接器将密封面平面度控制在0.005mm以内,配合面粗糙度Ra≤0.4μm,确保密封圈均匀受力。
应力分散:通过有限元分析优化接头结构,避免局部应力集中。例如,某超高压连接器采用分体式设计,将压力分散至多个支撑点,使最大应力降低60%。
防脱锁紧:安全锁紧装置需承受高压下的轴向拉力。某液压测试连接器采用双棘轮锁紧机构,在80MPa压力下可承受10吨级拉力,防止意外脱落。
3. 表面处理:抗腐蚀与耐磨性提升
高压环境下的介质腐蚀与机械磨损是连接器失效的主因。表面处理技术包括:
硬质阳极氧化:提升铝合金表面硬度至HV400以上,耐腐蚀性提升10倍。
陶瓷涂层:某深海连接器采用热喷涂氧化铝涂层,厚度50μm,硬度达HV1200,显著降低海水腐蚀速率。
自润滑涂层:在密封面喷涂聚四氟乙烯复合涂层,摩擦系数降低至0.05,延长密封圈寿命。
三、实践应用:从极端测试到工业场景的验证
1. 超高压液压测试场景
在液压元件测试中,连接器需承受瞬时高压冲击。某型号连接器通过优化密封圈材料与结构设计,在70MPa压力下实现M42×2.0外螺纹的可靠连接,实验室测试显示其可承受80-100MPa压力无泄漏。其核心创新包括:
密封圈预压缩量控制:通过精密模具将密封圈压缩率控制在15%-20%,避免过度压缩导致材料疲劳。
动态应力模拟:利用有限元分析优化接头壁厚分布,使应力集中系数降低至1.2以下。
2. 高温高压蒸汽清洗场景
在食品加工与汽车制造领域,连接器需耐受高温高压蒸汽。某工业清洗设备连接器采用梯度密封设计,在80℃、100Bar蒸汽冲击下,通过以下技术实现零泄漏:
硅橡胶密封圈:压缩形变率控制在5%以内,长期使用后密封性能无衰减。
螺旋卡口结构:通过机械自锁补偿热膨胀导致的间隙变化。
3. 深海探测与极地作业场景
在深海与极地环境中,连接器需应对高压、低温与腐蚀性介质。某深海连接器通过以下设计实现3000米水压下的稳定工作:
钛合金外壳:抗拉强度≥800MPa,耐海水腐蚀速率≤0.01mm/年。
多级密封系统:结合锥形密封圈与平面密封面,在30MPa压力下泄漏率低于1×10?? Pa·m?/s。
低温润滑脂:在-55℃环境下保持密封圈柔韧性,避免脆化。
四、未来趋势:智能化与模块化设计
随着工业4.0的推进,高压连接器正朝着智能化与模块化方向发展。例如,某新型连接器集成压力传感器与温度监测模块,可实时反馈密封状态;模块化设计支持快速更换密封组件,适应不同工况需求。此外,3D打印技术的应用使复杂密封结构制造成为可能,进一步提升了高压连接器的性能边界。
高压环境对快速密封连接器提出了严苛挑战,但通过材料创新、结构优化与工艺升级,现代连接器已能稳定工作于70MPa以上压力场景。未来,随着智能化与模块化技术的融合,连接器将在更广泛的工业领域中发挥关键作用,为高压系统的安全运行提供坚实保障。