在工业流体传输、电子设备检测及汽车制造等领域,快速密封连接器因其高效便捷的连接特性被广泛应用。其核心功能在于通过可靠的密封结构防止流体泄漏,而密封材料的选择直接决定了连接器的性能表现。本文将从材料特性、应用场景及维护策略三个维度,探讨快速密封连接器中密封材料的科学选型方法。
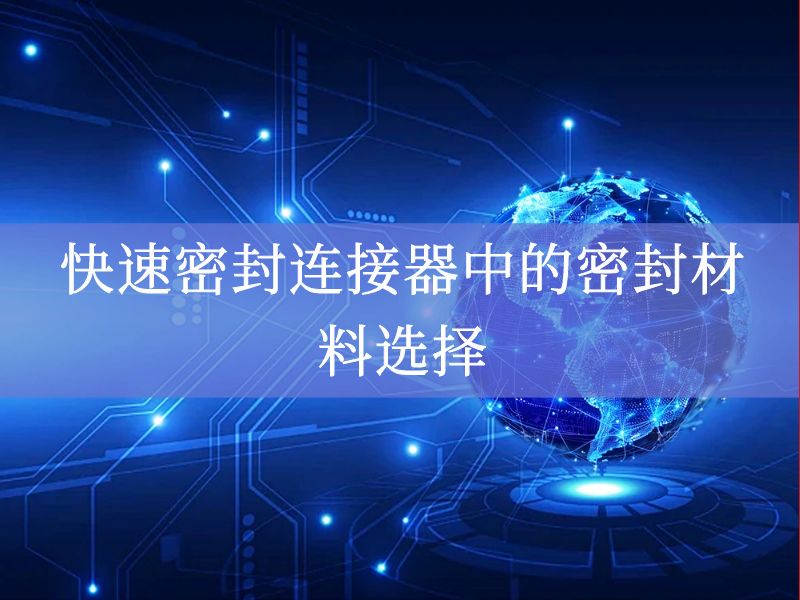
一、密封材料的物理化学特性分析
1. 弹性变形能力与密封压力
密封材料需具备优异的弹性变形能力,以适应不同管径的公差范围。以O型密封圈为例,其截面直径与沟槽尺寸的配合精度直接影响密封效果。当连接器插入管道时,密封圈通过压缩变形填充接触面间隙,形成动态密封层。实验数据显示,在高压环境下,弹性模量较低的橡胶材料(如丁腈橡胶)可通过15%-25%的压缩率实现有效密封,而硬度较高的聚四氟乙烯(PTFE)则需要更精确的尺寸匹配。
2. 耐温性能与介质兼容性
不同工况对密封材料的耐温范围提出差异化要求。例如,在汽车发动机冷却系统测试中,连接器需承受-40℃至 150℃的极端温度变化,此时硅橡胶因其-60℃至 230℃的宽温域特性成为优选。而在燃油系统测试中,丁腈橡胶凭借对矿物油和柴油的优异耐受性,成为主流密封材料。需注意的是,氯丁橡胶在低温环境下易结晶硬化,不适用于极寒环境。
3. 耐磨性与抗老化性能
流体冲刷和机械摩擦是导致密封失效的主要因素。通过表面硬化处理或添加碳纤维增强材料,可显著提升橡胶材料的耐磨性。例如,添加20%碳纤维的丁腈橡胶,其阿克隆磨耗量可降低至0.1cm?/1.61km以下。此外,采用氟橡胶等抗臭氧材料,可有效延长户外使用场景下的密封寿命。
二、典型应用场景的材料适配方案
1. 工业流体传输系统
在化工管道检测中,连接器需承受强腐蚀性介质(如硫酸、氢氧化钠)的侵蚀。此时应选用氟橡胶或全氟醚橡胶,其耐化学腐蚀性能可覆盖PH值0-14的介质范围。对于高压蒸汽传输系统,需采用金属对金属密封结构配合石墨填料,确保在350℃高温下仍能维持0.1MPa以下的泄漏率。
2. 汽车制造与测试
在新能源汽车电池包气密性检测中,连接器需满足IP67防护等级要求。采用硅橡胶密封圈配合双唇口结构设计,可在0.3MPa测试压力下实现零泄漏。对于燃油系统高压共轨测试,需选用氢化丁腈橡胶(HNBR),其耐油性能较普通丁腈橡胶提升30%,且可在150℃高温下长期使用。
3. 电子设备检测
在半导体设备真空腔体连接中,连接器需满足10?? Pa·m?/s级别的漏率要求。此时应采用全金属密封结构配合铜垫片,通过机械加工实现微米级平面度控制。对于消费电子产品的防水测试,TPU(热塑性聚氨酯)密封圈因其低压缩永久变形率(<5%),可确保5000次插拔后的密封性能衰减小于10%。
三、密封系统的维护与优化策略
1. 定期检测与寿命评估
建立密封件状态监测体系,通过红外热成像检测密封区域温度异常,或采用超声波泄漏检测仪定位微小泄漏点。对于关键设备,建议每2000工作小时进行密封圈硬度测试(邵氏A硬度计),当硬度变化超过10%时应及时更换。
2. 智能密封材料研发
新型形状记忆合金密封件可通过温度刺激实现自修复功能。实验表明,含镍钛合金的复合密封材料在发生微裂纹后,经80℃加热可恢复90%以上的密封性能。此外,自愈合聚合物密封剂在微损伤时可自动释放修复剂,延长密封寿命3-5倍。
3. 标准化与模块化设计
推行密封件标准化体系,建立包含尺寸、材料、性能参数的数据库。例如,将O型圈截面直径标准化为1.8mm、2.65mm、3.55mm等规格,配套开发通用型沟槽设计工具。模块化设计可降低30%以上的备件成本,同时提升维护效率。
四、材料选型的决策模型
构建包含工况参数(温度、压力、介质)、性能指标(泄漏率、寿命)、经济因素(采购成本、维护费用)的三维决策模型。例如,在高温蒸汽场景中,金属密封方案虽初期成本较高,但因免维护特性,全生命周期成本较橡胶密封方案降低40%。通过该模型,可实现从经验选型到数据驱动决策的转变。
密封材料的选择是快速密封连接器设计的核心环节。随着材料科学的进步,新型复合材料、智能材料正逐步改变传统选型逻辑。未来,通过建立材料性能数据库、开发自适应密封结构,可实现密封系统的智能化升级,为工业4.0时代的流体传输提供更可靠的保障。