在工业流体传输与设备连接领域,快速密封连接器凭借其高效、可靠的特性,成为保障系统稳定运行的关键部件。其核心密封原理基于弹性密封件与机械结构的协同作用,通过多重密封机制实现零泄漏连接,满足不同工况下的密封需求。以下从密封结构、材料选择、工作机制及维护要点四个维度展开分析。
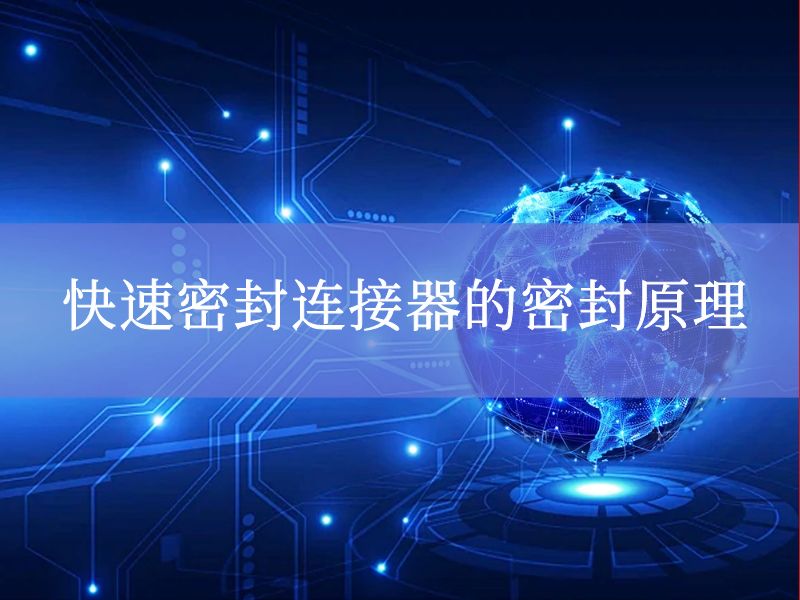
一、弹性密封件的核心作用
快速密封连接器的密封性能主要依赖于弹性密封件的弹性变形能力。O型密封圈作为最常见的密封元件,通过其独特的环形结构与材料特性,在连接过程中实现动态密封。当连接器插入时,O型密封圈受到径向挤压,产生弹性形变,其表面与连接件内壁形成紧密贴合,形成第一道密封屏障。这种密封机制不仅适用于常温常压环境,更能在高温、高压或高速流体工况下保持稳定。例如,在液压系统中,O型密封圈可承受超过30MPa的压力,且在-50℃至150℃温度范围内维持弹性。
除O型密封圈外,锥形密封圈与平面密封面亦为常见密封形式。锥形密封圈通过斜面接触设计,在插入过程中自动调整贴合角度,适用于管径公差较大的连接场景;平面密封面则通过端面压紧实现密封,其结构简单、加工成本低,广泛应用于低压工况。例如,在气动系统中,平面密封面可承受0.1MPa至1MPa的压力,且对连接端面平整度要求较低。
二、机械结构的协同密封机制
快速密封连接器的密封性能并非单一依赖密封件,而是通过机械结构与密封件的协同作用实现。连接器通常由插头、插座及锁紧装置三部分构成。插头端部集成密封圈,插座内部设计与之匹配的金属接触面,当插头插入时,密封圈与接触面形成双重密封。锁紧装置则通过机械锁定确保连接稳定性,防止因流体压力波动导致连接松动。
以某型连接器为例,其锁紧装置采用自动锁定与手动释放双重设计。插入时,插头推动锁紧滑块自动卡入插座凹槽,实现快速锁定;拆卸时,通过按压释放按钮即可解除锁定。这种设计使连接器在承受10MPa压力时仍能保持零泄漏,且单次连接/拆卸时间可缩短至3秒以内。此外,部分连接器还集成自锁式阀门,在断开连接时自动切断流体通路,避免介质泄漏或污染。
三、密封材料的适配性选择
密封材料的性能直接影响连接器的适用范围与寿命。常见密封材料包括硅胶、丁腈橡胶、氯丁橡胶等,其特性需与工况环境匹配。例如,丁腈橡胶因其优异的耐油性与耐磨性,广泛应用于燃油、液压油等介质传输系统;氯丁橡胶则因耐候性强、抗老化性能突出,适用于户外或高温环境。在某化工项目中,连接器采用氟橡胶密封圈,成功抵御强酸强碱腐蚀,使用寿命延长至5年以上。
材料选择需综合考虑介质类型、温度范围及压力等级。例如,在低温工况下,硅胶密封圈因耐寒性佳(-60℃仍保持弹性)成为首选;而在高温高压场景中,聚四氟乙烯密封件因耐温性高(260℃)且化学稳定性强,可确保长期密封可靠性。此外,密封圈的硬度、压缩永久变形率等参数亦需严格匹配,以避免因材料老化导致泄漏。
四、密封性能的动态维护
快速密封连接器的长期可靠性依赖于定期维护与检测。密封圈作为易损件,需根据使用频率与工况环境制定更换周期。例如,在高频次插拔场景中,O型密封圈的压缩永久变形率可能加速上升,建议每500次插拔后检查密封性能。检测方法包括压力测试、泄漏率检测及目视检查,其中泄漏率检测标准通常要求≤0.1mL/min。
更换密封圈时,需确保新密封圈尺寸与原型号一致,并清洁连接面以避免杂质嵌入。对于平面密封面,需检查其平整度与光洁度,必要时进行研磨修复。此外,锁紧装置的润滑与紧固亦需定期维护,以防止机械磨损导致连接失效。例如,在某汽车制造产线中,通过建立连接器维护台账,将连接器故障率降低至0.3%以下。
五、密封原理的工程应用案例
在某航空发动机测试系统中,连接器需承受高温高压燃油的冲击。通过采用耐高温氟橡胶密封圈与锥形密封面设计,连接器在200℃、15MPa工况下实现零泄漏,且单次连接时间缩短至2秒。在某半导体生产线中,连接器需适应超纯水传输的洁净度要求。通过采用全金属密封结构与平面密封面设计,连接器颗粒物释放量控制在Class 1级别以下,满足半导体工艺需求。
在某新能源电池测试平台中,连接器需频繁插拔以更换测试样品。通过集成自动锁定装置与快速更换密封圈设计,连接器插拔寿命提升至10万次以上,且泄漏率始终≤0.05mL/min。这些案例表明,快速密封连接器的密封原理需与具体工况深度匹配,方能实现性能与成本的平衡。
结语
快速密封连接器的密封原理是弹性密封件、机械结构与材料科学的综合体现。通过优化密封件设计、匹配材料特性、强化机械锁定及建立维护体系,可确保连接器在复杂工况下实现长期稳定运行。未来,随着工业自动化与智能化的发展,连接器将向更高压力、更高温度、更小体积方向演进,其密封原理亦需持续创新,以适应新能源、半导体、航空航天等领域的严苛需求。