在工业生产与设备维护中,气密性与水密性是衡量产品性能的关键指标。快速密封连接器作为连接与密封的核心部件,通过创新的结构设计与材料应用,实现了高效、可靠的密封效果。本文将从技术原理、结构类型、应用场景及维护要点四个维度,深入解析快速密封连接器如何实现气密性与水密性。
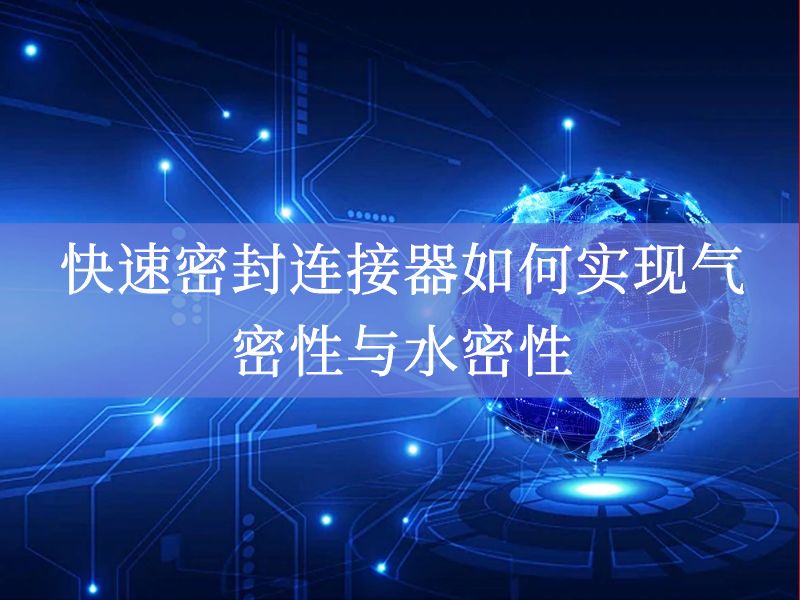
一、密封原理:多技术协同实现零泄漏
快速密封连接器的核心目标是通过物理或化学手段,在连接部位形成稳定的密封屏障,阻止气体或液体的渗透。其技术实现主要依赖以下三类原理:
1. 弹性形变密封
利用橡胶、硅胶等弹性材料的形变特性,通过外力挤压使密封件与连接面紧密贴合。例如,在直管测试中,连接器内置的弹性密封圈在插入管口后,受径向压力膨胀,填充管壁与连接器之间的间隙,形成动态密封。此类密封方式对管壁粗糙度要求较低,适用于非标尺寸或表面粗糙的工件。
2. 机械自锁密封
通过滚珠、卡扣等机械结构实现自锁。例如,针对带凸起的非标管口,连接器内部设计滚珠导向槽,当管口插入时,滚珠在弹簧作用下卡入凹槽,同时密封圈被压缩形成端面密封。这种设计可避免划伤工件表面,且操作简便,适用于空间受限或需频繁拆装的场景。
3. 气压驱动密封
部分连接器采用气压驱动密封圈膨胀的原理。在自动化测试中,连接器插入工件后,通过气孔通入压缩空气,推动密封圈向外扩张,抱紧管壁。此方式适用于高压测试,且可与自动化工装集成,显著提升测试效率。
二、结构类型:适配多样化需求
根据应用场景的不同,快速密封连接器衍生出多种结构类型,每种类型均针对特定工况优化设计。
1. 内胀式连接器
专为直管、钻孔及内螺纹部件设计。其密封件采用弹性材料,通过摩擦力实现连接。例如,在汽车发动机冷却系统测试中,内胀式连接器可快速插入冷却管路,无需额外夹具,且能适应不同内径的管件。
2. 螺纹式连接器
适用于外螺纹部件的密封测试。通过前端O型圈与工件端面贴合实现密封,对端面粗糙度要求较高。例如,在阀门气密性测试中,螺纹式连接器可快速旋入阀体,形成端面密封,避免传统卡箍连接可能导致的泄漏风险。
3. 滚珠式连接器
针对非标管口设计,通过内部滚珠导向与自锁机制实现密封。例如,在医疗器械管件测试中,滚珠式连接器可避免划伤管壁,同时确保密封可靠性。
4. 平面密封连接器
适用于管道或设备的端面密封。通过平面之间的压紧力形成密封层,适用于低压、低速环境。例如,在水泵进出口连接中,平面密封连接器可快速实现端面密封,且拆卸后密封面无损伤。
三、应用场景:覆盖多行业需求
快速密封连接器凭借其高效性与可靠性,在多个行业中得到广泛应用。
1. 工业检漏测试
在焊接、粘接等工艺后,需对产品进行气密性检测。例如,在大型容器组焊过程中,中间过程的检漏至关重要。快速密封连接器可快速连接复杂管口,避免传统卡箍连接可能导致的误判与返工。
2. 新能源汽车测试
新能源汽车的“三电系统”需进行大量气密性测试。例如,电池包冷却系统需测试水道密封性,电机控制器需检测外壳气密性。快速密封连接器可快速连接进出水管、螺纹孔等,满足自动化测试需求。
3. 医疗器械生产
医疗器械对密封性要求极高。例如,输液管、呼吸机管路等需进行气密性与水密性测试。快速密封连接器可避免划伤管壁,同时确保密封可靠性,符合医疗行业标准。
4. 航空航天领域
航空航天设备需在极端环境下运行,对密封性要求严苛。例如,飞机燃油系统需测试管路密封性,卫星电子设备需防水防尘。快速密封连接器通过高强度材料与精密设计,满足IP68及以上防护等级要求。
四、维护与优化:延长使用寿命
为确保快速密封连接器的长期可靠性,需定期进行维护与优化。
1. 密封面检查
每次使用前,需检查密封面是否有划痕、变形或异物。例如,在医疗管件测试中,密封面损伤可能导致泄漏,需及时更换密封件。
2. 密封材料更换
弹性密封材料随使用时间延长会老化,需定期更换。例如,在高压测试中,密封圈老化可能导致泄漏率上升,需按厂家建议周期更换。
3. 自动化工装校准
自动化测试中,需定期校准气缸压力、插入深度等参数。例如,在汽车部件测试中,气缸压力不足可能导致密封不严,需通过压力传感器监测并调整。
4. 非标定制优化
针对特殊工件,需进行非标定制。例如,在异形管口测试中,可通过3D建模优化连接器结构,确保密封性与操作便捷性。
五、未来趋势:智能化与集成化
随着工业4.0的推进,快速密封连接器正朝着智能化与集成化方向发展。例如,部分连接器已集成压力传感器与无线通信模块,可实时监测密封状态并上传数据。此外,模块化设计使连接器可快速更换密封件或适配不同工件,进一步提升生产效率。
快速密封连接器通过弹性形变、机械自锁与气压驱动等原理,结合内胀式、螺纹式、滚珠式等多种结构,实现了高效、可靠的气密性与水密性。其在工业检漏、新能源汽车、医疗器械等领域的广泛应用,证明了其技术价值。未来,随着智能化与集成化技术的融合,快速密封连接器将为工业生产提供更强大的支持。