一、化工行业对连接器的核心需求
化工行业因其生产环境的特殊性,对设备连接器的性能提出了严苛要求。生产过程中涉及的强酸、强碱、有机溶剂等腐蚀性介质,以及高温、高压、高湿度等极端工况,要求连接器必须具备卓越的防腐能力。此外,化工生产对设备可靠性和安全性的高依赖性,进一步凸显了连接器防腐设计的重要性。一旦连接器因腐蚀导致密封失效或电气故障,可能引发介质泄漏、设备停机甚至安全事故,造成不可估量的经济损失。
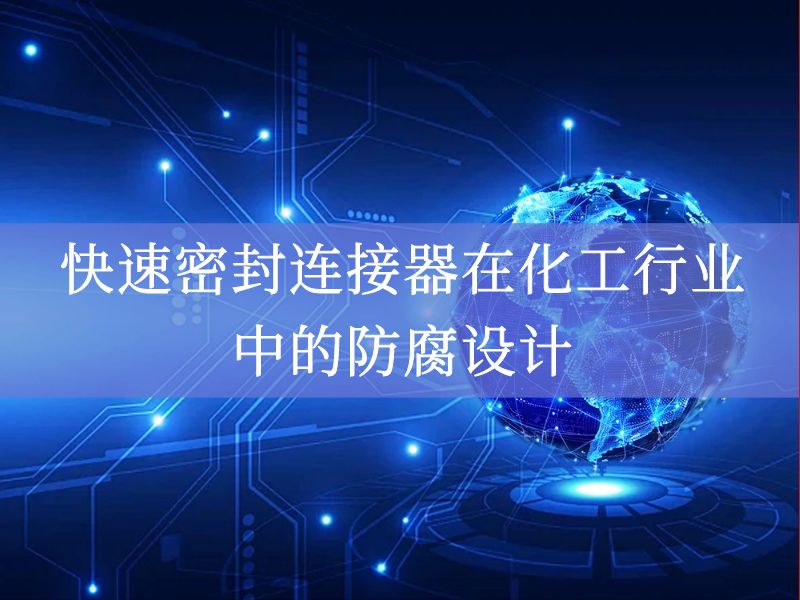
二、防腐设计的核心要素
(一)材料选择
连接器的防腐性能与其材料选择密切相关。在化工场景中,金属材料需具备高耐蚀性,如316不锈钢因其优异的抗点蚀和缝隙腐蚀能力,成为化工连接器的常用基材。非金属材料方面,聚四氟乙烯(PTFE)等高分子材料凭借其化学惰性、低摩擦系数和耐温性,被广泛应用于密封件和绝缘部件。例如,某连接器采用PTFE密封圈,在强酸环境中长期使用后仍能保持弹性,确保密封性能。
(二)表面处理技术
表面处理是提升连接器抗腐蚀性的关键手段。金属涂层技术通过电镀、热浸镀等方式,在基材表面形成致密的金属保护层。例如,镀镍层可有效隔绝腐蚀介质,而镀铬层则兼具耐磨性和耐蚀性。非金属涂层则通过喷涂防腐涂料或陶瓷涂层,进一步增强材料的抗腐蚀能力。例如,某连接器采用环氧树脂涂层,在盐雾测试中表现出色,显著延长了使用寿命。
(三)密封结构设计
密封结构是连接器防腐设计的核心。O型密封圈通过弹性变形与接触面紧密贴合,形成可靠的密封层。其优势在于结构简单、适应性强,可在高温、高压环境下稳定工作。平面密封面则通过机械压力实现端面密封,适用于低压、低速场景。例如,某连接器采用双重密封设计,结合O型圈与平面密封,在高压气体输送中实现了零泄漏。
(四)结构优化与工艺改进
连接器的结构设计需兼顾防腐与功能性。通过优化接触面形状、增加密封圈压缩量,可提升密封效果。例如,某连接器采用锥形密封圈设计,自动适应接触面形变,降低了安装难度。工艺方面,精密加工和表面抛光可减少微观缺陷,避免腐蚀介质残留。例如,某连接器通过激光焊接工艺,实现了外壳的无缝连接,彻底杜绝了介质渗透风险。
三、典型应用场景与案例分析
(一)强酸强碱环境
在硫酸、氢氧化钠等强腐蚀介质输送中,连接器需承受高浓度化学物质的侵蚀。某化工厂采用全塑外壳连接器,其外壳采用高性能工程塑料,在强酸环境中使用两年后仍保持完好。密封结构方面,该连接器采用双O型圈设计,配合氟橡胶密封圈,实现了耐温-40℃至200℃的宽温域密封。
(二)高温高压环境
在石油炼化、合成氨等高温高压工艺中,连接器需承受极端工况。某炼油厂采用金属密封连接器,其密封面采用硬质合金堆焊技术,硬度达HRC65以上,有效抵抗高温磨损。此外,该连接器通过优化流道设计,降低了介质对密封面的冲刷,延长了使用寿命。
(三)有机溶剂环境
在涂料、制药等有机溶剂输送中,连接器需具备耐溶剂性。某制药企业采用PTFE全包覆连接器,其内部金属部件完全被PTFE覆盖,避免了溶剂与金属的直接接触。实验表明,该连接器在甲苯、丙酮等溶剂中浸泡30天后,仍能保持密封性能。
四、防腐设计的验证与优化
(一)实验室测试
盐雾测试是评估连接器耐蚀性的重要手段。某连接器通过48小时中性盐雾测试,表面腐蚀面积小于5%,达到行业领先水平。此外,高温老化测试可模拟长期使用环境,某连接器在150℃高温下持续工作1000小时后,密封性能未出现衰减。
(二)现场应用反馈
某化工企业反馈,采用优化后的连接器后,设备停机时间减少了60%。通过定期巡检发现,连接器表面无腐蚀迹象,密封圈弹性良好。此外,用户还提出改进建议,如增加防呆设计以避免误操作,这些反馈为后续产品迭代提供了方向。
(三)持续改进方向
未来,连接器防腐设计将向智能化、模块化方向发展。例如,集成传感器实时监测密封状态,通过无线传输将数据上传至云端。模块化设计则允许用户根据工况更换密封件或外壳,降低维护成本。此外,新型纳米涂层技术有望进一步提升材料的耐蚀性。
五、行业趋势与未来展望
随着化工行业向绿色化、智能化转型,连接器防腐设计面临新的挑战与机遇。一方面,环保法规对设备泄漏率的要求日益严格,推动连接器向零泄漏方向发展。另一方面,工业互联网的普及要求连接器具备更高的可靠性和可维护性。未来,连接器将与传感器、执行器深度融合,形成智能连接系统,为化工生产提供更安全、高效的解决方案。
结语
快速密封连接器的防腐设计是化工行业设备可靠性的关键保障。通过材料创新、结构优化和工艺改进,连接器在极端工况下的性能得到了显著提升。未来,随着新材料、新技术的应用,连接器防腐设计将不断突破,为化工行业的安全生产和可持续发展提供更强有力的支持。