在工业生产与设备运行中,高温环境对连接器的性能提出了严苛挑战。快速密封连接器作为一种兼具高效连接与可靠密封特性的装置,凭借其独特的技术优势,在高温场景中展现出显著的应用价值。其核心功能不仅在于实现设备的快速拆装,更在于确保在极端温度下仍能维持稳定的密封效果,从而保障系统的安全运行。
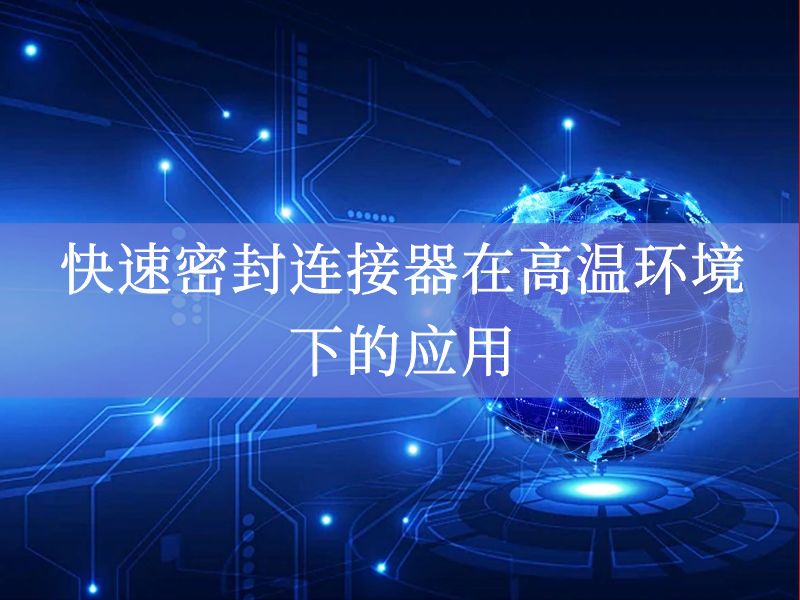
高温环境对连接器的核心挑战
高温环境对连接器的性能影响主要体现在材料形变、密封失效及电气性能下降三个方面。在持续高温条件下,普通连接器的金属部件可能因热膨胀导致尺寸变化,进而引发接触不良或松动;橡胶类密封件则可能因软化或老化失去弹性,导致介质泄漏。此外,高温还可能加速连接器内部绝缘材料的分解,降低其电气绝缘性能,增加短路风险。这些挑战在航空航天、石油化工、电力设备等领域尤为突出,例如航空发动机的燃油管路、炼油厂的蒸馏塔管道、核电站的冷却系统等,均需在高温条件下长期稳定运行。
快速密封连接器的技术突破
为应对高温挑战,快速密封连接器通过材料创新与结构优化实现了技术突破。在材料选择上,采用耐高温合金作为主体结构,如某些镍基合金可在600℃以上环境中保持强度与稳定性;密封件则选用氟橡胶或聚四氟乙烯等特种材料,其耐温范围可达250℃至300℃,且具备优异的抗化学腐蚀能力。在结构设计上,部分连接器采用双层密封结构,通过金属与橡胶的复合密封实现冗余保护;内胀式设计则利用金属弹性变形实现自锁紧,避免因热膨胀导致的松动。例如,某型号连接器通过优化密封圈的截面形状与压缩比,使其在高温下仍能保持0.1mm级的高精度密封。
航空航天领域的典型应用
在航空航天领域,快速密封连接器被广泛应用于发动机燃油系统、液压管路及环境控制系统。以航空发动机为例,其燃油喷嘴需在高温高压环境下持续工作,传统连接方式难以满足快速维护需求。某新型连接器通过集成快速锁紧机构与耐高温密封技术,实现了燃油管路的秒级拆装,同时将泄漏率控制在10?? Pa·m?/s以下。在某型客机的液压系统中,连接器需承受-55℃至150℃的极端温差,通过采用金属波纹管密封与自补偿结构,有效解决了热胀冷缩导致的密封失效问题,使系统维护时间缩短了60%。
石油化工行业的实践案例
石油化工行业的反应釜、蒸馏塔等设备常处于200℃以上的高温环境,且介质多为强腐蚀性化学品。某炼油厂在催化裂化装置中采用耐高温快速密封连接器,替代了传统的法兰连接方式。该连接器通过陶瓷涂层增强抗腐蚀性能,配合石墨密封环实现350℃下的零泄漏。在某化工厂的聚乙烯生产线上,连接器需承受280℃的高温与频繁的工艺切换,通过优化密封面的表面粗糙度与硬度匹配,将密封寿命延长至传统方案的3倍以上,同时减少了因泄漏导致的停机损失。
电力设备中的创新应用
在电力设备领域,快速密封连接器主要应用于高温电缆接头、变压器冷却系统及核电站管道。某超临界火电厂的锅炉给水泵系统采用耐高温连接器,实现了电缆与电机的高效连接。该连接器通过液态金属填充技术填补接触间隙,将接触电阻降低了80%,同时通过陶瓷绝缘套管承受1000℃以上的高温。在核电站的冷却水系统中,连接器需承受放射性环境与高温高压的双重考验,通过采用双层金属密封与氦气检漏技术,将泄漏率控制在10??? Pa·m?/s以下,确保了核安全。
技术优势与未来发展方向
快速密封连接器在高温环境下的技术优势主要体现在三个方面:一是快速拆装能力,通过自锁紧机构或快插设计,使维护时间缩短至传统方案的1/5;二是高可靠性,通过冗余密封结构与耐高温材料,将泄漏率降低至10??? Pa·m?/s量级;三是长寿命,通过抗疲劳设计与自润滑材料,使连接器在高温循环工况下的寿命达到10万次以上。未来,随着材料科学与智能制造技术的发展,连接器将向更高温度(如800℃以上)、更小体积(如微型化设计)及智能化(如集成温度传感器)方向演进。例如,某研究机构正在开发基于形状记忆合金的智能连接器,可通过温度变化自动调整密封压力,进一步提升高温环境下的适应性。
结语
快速密封连接器通过材料创新、结构优化与工艺改进,成功解决了高温环境下的连接与密封难题。其在航空航天、石油化工、电力设备等领域的广泛应用,不仅提升了系统运行的可靠性与维护效率,也为极端工况下的设备设计提供了新的解决方案。随着技术的持续进步,快速密封连接器将在更多高温场景中发挥关键作用,推动工业设备向更高性能、更安全可靠的方向发展。